Industrial Engine Maintenance: A Comprehensive Guide To Keep Your Machinery Running Smoothly
In the world of industrial operations, industrial engine maintenance plays a crucial role in ensuring machinery runs efficiently and effectively. Proper maintenance not only extends the lifespan of the equipment but also enhances productivity and reduces downtime. In this article, we will explore the key aspects of maintaining industrial engines, including best practices, common challenges, and strategies to optimize performance.
Whether you're managing a small workshop or overseeing a large manufacturing facility, understanding the importance of industrial engine maintenance is essential. Neglecting this aspect can lead to costly repairs, equipment failure, and even safety hazards for your workforce. By investing in regular maintenance, you can protect your assets and maintain operational excellence.
This guide aims to provide valuable insights into the world of industrial engine maintenance. From understanding the basics to implementing advanced techniques, we'll cover everything you need to know to keep your machinery in top condition. Let's dive in!
Read also:Lawrence Odonnell Wife A Closer Look At The Woman Behind The Iconic Tv Host
Table of Contents
- The Importance of Industrial Engine Maintenance
- Understanding the Basics of Engine Maintenance
- Types of Industrial Engines and Their Maintenance Needs
- Creating an Effective Maintenance Schedule
- Advanced Techniques in Industrial Engine Maintenance
- Essential Tools and Equipment for Maintenance
- Common Challenges in Engine Maintenance
- Cost Implications of Neglecting Maintenance
- Safety Considerations in Industrial Engine Maintenance
- The Future of Industrial Engine Maintenance
The Importance of Industrial Engine Maintenance
Industrial engine maintenance is more than just a routine task; it's a strategic investment in the longevity and efficiency of your machinery. Without proper maintenance, engines can suffer from wear and tear, leading to reduced performance and increased downtime. Regular maintenance ensures that all components are functioning optimally, preventing costly repairs and extending the lifespan of the equipment.
Moreover, maintaining industrial engines aligns with the principles of YMYL (Your Money or Your Life), as it directly impacts the safety and financial well-being of your business. By prioritizing maintenance, you safeguard your operations and protect your workforce from potential hazards.
According to a report by the U.S. Department of Energy, companies that implement a structured maintenance program can reduce energy consumption by up to 20% and decrease maintenance costs by 30%. These statistics underscore the importance of investing in regular maintenance practices.
Understanding the Basics of Engine Maintenance
Key Components of Industrial Engines
Before diving into maintenance strategies, it's essential to understand the key components of industrial engines. These include:
- Pistons and cylinders
- Crankshaft and camshaft
- Valves and valve train
- Cooling and lubrication systems
Each component plays a vital role in the engine's operation, and their condition directly affects overall performance. Regular inspection and maintenance of these parts are critical to ensuring smooth functioning.
Basic Maintenance Practices
Some fundamental practices in industrial engine maintenance include:
Read also:Anja Ravello The Rising Star Whorsquos Redefining Fashion And Beauty Standards
- Regular oil changes to ensure proper lubrication
- Cleaning and inspecting air filters
- Checking coolant levels and quality
- Monitoring for leaks and unusual noises
Implementing these basic practices can significantly improve engine performance and reliability.
Types of Industrial Engines and Their Maintenance Needs
Industrial engines come in various types, each with unique maintenance requirements. The most common types include:
- Diesel engines
- Gasoline engines
- Electric motors
- Turbine engines
Diesel engines, for instance, require regular fuel system maintenance to prevent clogging and ensure efficient combustion. Gasoline engines, on the other hand, may need more frequent spark plug replacements. Understanding the specific needs of each engine type is crucial for effective maintenance.
Creating an Effective Maintenance Schedule
Factors to Consider
Developing a maintenance schedule involves considering several factors, such as:
- Engine type and model
- Operating conditions
- Manufacturer recommendations
- Historical data on equipment performance
By analyzing these factors, you can create a tailored schedule that addresses the unique needs of your machinery.
Implementing a Preventive Maintenance Plan
A preventive maintenance plan involves regular inspections and servicing to identify and address potential issues before they escalate. This approach not only reduces downtime but also minimizes repair costs. Key components of a preventive maintenance plan include:
- Regular inspections and testing
- Scheduled part replacements
- Training for maintenance personnel
Adopting a preventive maintenance strategy can significantly enhance the reliability and efficiency of your industrial engines.
Advanced Techniques in Industrial Engine Maintenance
Condition Monitoring
Condition monitoring involves using advanced technologies to assess the health of industrial engines in real-time. Techniques such as vibration analysis, oil analysis, and thermography can detect early signs of wear and tear, enabling proactive maintenance.
Predictive Maintenance
Predictive maintenance leverages data analytics and machine learning algorithms to predict when maintenance is required. By analyzing performance data, this approach can optimize maintenance schedules and reduce unnecessary interventions.
Essential Tools and Equipment for Maintenance
Having the right tools and equipment is crucial for effective industrial engine maintenance. Some essential items include:
- Diagnostic tools for engine testing
- Lubrication equipment
- Specialized wrenches and sockets
- Safety gear for maintenance personnel
Investing in high-quality tools not only improves maintenance efficiency but also ensures the safety of your team.
Common Challenges in Engine Maintenance
Despite the importance of industrial engine maintenance, several challenges can hinder its effectiveness. These include:
- Lack of skilled personnel
- Insufficient budget for maintenance
- Difficulty in sourcing spare parts
- Inadequate training for maintenance staff
Addressing these challenges requires a strategic approach, including investing in employee training and collaborating with reliable suppliers.
Cost Implications of Neglecting Maintenance
Neglecting industrial engine maintenance can have significant financial repercussions. Unplanned downtime, emergency repairs, and reduced equipment lifespan can lead to substantial costs. According to a study by the Aberdeen Group, companies that neglect maintenance spend 30% more on repairs than those with proactive maintenance programs.
Furthermore, inadequate maintenance can result in safety hazards, leading to potential legal liabilities and reputational damage. By prioritizing maintenance, you can mitigate these risks and ensure the financial stability of your operations.
Safety Considerations in Industrial Engine Maintenance
Safety should always be a top priority when performing industrial engine maintenance. Key safety considerations include:
- Wearing appropriate personal protective equipment (PPE)
- Following lockout/tagout procedures
- Ensuring proper ventilation in work areas
- Providing regular safety training for maintenance personnel
By adhering to these safety practices, you can protect your workforce and maintain a safe working environment.
The Future of Industrial Engine Maintenance
The field of industrial engine maintenance is evolving rapidly, driven by advancements in technology and increasing demands for efficiency. Emerging trends such as IoT-enabled monitoring systems, AI-driven diagnostics, and sustainable maintenance practices are shaping the future of this industry.
As businesses strive to reduce their carbon footprint, there is a growing focus on eco-friendly maintenance solutions. This includes using biodegradable lubricants and implementing energy-efficient practices. Embracing these innovations can position your organization as a leader in sustainable industrial operations.
Conclusion
In conclusion, industrial engine maintenance is a critical component of operational success. By understanding the basics, implementing effective maintenance strategies, and leveraging advanced technologies, you can ensure the longevity and efficiency of your machinery. Remember, neglecting maintenance can lead to costly repairs, safety hazards, and reduced productivity.
We encourage you to take action by creating a comprehensive maintenance plan for your industrial engines. Share your thoughts and experiences in the comments below, and don't forget to explore our other articles for more insights into industrial operations. Together, let's build a safer, more efficient future for your business!

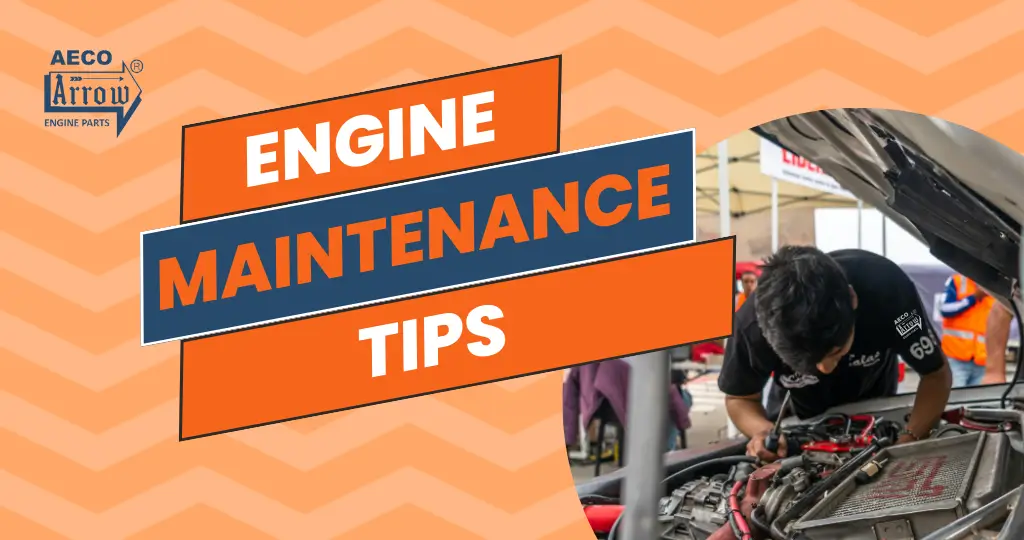
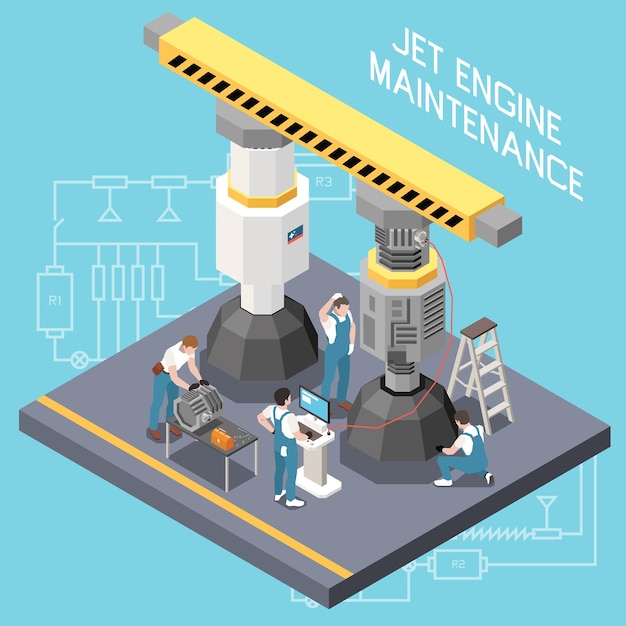