Comprehensive Guide To Types Of Knuckles: Understanding Their Functions And Applications
Knuckles play a crucial role in various mechanical systems, serving as vital connectors and joints that enable movement and flexibility. Whether you're working on automotive repairs, plumbing projects, or engineering designs, understanding the different types of knuckles is essential for selecting the right component for your needs. This article delves into the world of knuckles, exploring their varieties, functions, and applications in detail.
From ball joints to universal joints, each type of knuckle has unique characteristics that make it suitable for specific tasks. By familiarizing yourself with these differences, you can ensure optimal performance and longevity of your mechanical systems. In this article, we will provide an in-depth exploration of the various types of knuckles, complete with technical insights and practical advice.
Our goal is to equip you with the knowledge necessary to make informed decisions when choosing the right knuckle for your projects. Let's dive into the fascinating world of knuckles and uncover the secrets behind their functionality and importance in modern engineering.
Read also:Minister Of Communications And Digital Technologies Fights For Creators To Get Paid By Tiktok
Table of Contents
- What Are Knuckles?
- Types of Knuckles
- Ball Joints
- Universal Joints
- Hooke Joints
- Constant Velocity Joints
- Trunnion Joints
- Bearing Knuckles
- Applications of Knuckles
- Maintenance Tips for Knuckles
- Common Issues and Solutions
- Conclusion
What Are Knuckles?
Knuckles are mechanical components designed to connect two or more parts, allowing for smooth movement and flexibility. These components are typically found in automotive suspensions, steering systems, and various industrial applications. The primary function of a knuckle is to facilitate angular motion while maintaining structural integrity.
The term "knuckle" refers to the joint-like structure that enables rotational and angular movement between connected parts. Depending on the application, knuckles can vary significantly in design and functionality. Understanding the basic principles of knuckles is essential for anyone working with mechanical systems.
Knuckles are often made from durable materials such as steel, aluminum, or composite materials, ensuring they can withstand significant stress and wear over time. Their design and material choice depend heavily on the specific application and environmental conditions.
Types of Knuckles
There are several types of knuckles, each designed for specific purposes and applications. Below, we will explore the most common types of knuckles and their unique characteristics:
- Ball joints
- Universal joints
- Hooke joints
- Constant velocity joints
- Trunnion joints
- Bearing knuckles
Each type of knuckle serves a distinct purpose, making it crucial to choose the right one based on your project's requirements. Let's dive deeper into each type to better understand their functions and applications.
Ball Joints
Ball joints are one of the most common types of knuckles, widely used in automotive steering and suspension systems. These joints consist of a ball-and-socket mechanism that allows for smooth, multidirectional movement. Ball joints are designed to withstand significant loads and provide reliable performance in demanding environments.
Read also:Olivia Black Actress Rising Star In The Spotlight
Key Features of Ball Joints
- Multidirectional movement
- High load-bearing capacity
- Compact design
- Long service life with proper maintenance
Ball joints are commonly found in vehicles, where they enable the wheels to move up and down while maintaining alignment with the steering system. Their durability and versatility make them an ideal choice for automotive applications.
Universal Joints
Universal joints, also known as U-joints, are another popular type of knuckle used in automotive and industrial applications. These joints allow for angular movement between two rotating shafts, enabling power transmission even when the shafts are not aligned.
Advantages of Universal Joints
- Allows for significant angular displacement
- Simple and cost-effective design
- High torque transmission capability
- Wide range of applications
Universal joints are commonly used in drive shafts, agricultural machinery, and other systems requiring flexible power transmission. Their ability to accommodate angular misalignment makes them indispensable in many mechanical systems.
Hooke Joints
Hooke joints, also known as Cardan joints, are similar to universal joints but offer improved performance in certain applications. These joints are designed to transmit rotational motion between two shafts at an angle, with the added advantage of providing more consistent velocity.
Characteristics of Hooke Joints
- Improved velocity consistency compared to standard U-joints
- Higher angular capacity
- Reliable performance in high-speed applications
- Commonly used in industrial machinery
Hooke joints are particularly well-suited for applications requiring precise control over rotational speed and torque. Their advanced design makes them a popular choice in industries such as aerospace and manufacturing.
Constant Velocity Joints
Constant velocity (CV) joints are specialized knuckles designed to transmit power smoothly and efficiently, even at significant angles. These joints are widely used in front-wheel-drive vehicles, where they enable the wheels to rotate at a constant speed regardless of the steering angle.
Benefits of Constant Velocity Joints
- Smooth and consistent power transmission
- High angular capacity
- Reduced vibration and noise
- Long service life with proper lubrication
CV joints are essential components in modern vehicles, ensuring optimal performance and ride comfort. Their ability to maintain constant velocity makes them indispensable in automotive applications.
Trunnion Joints
Trunnion joints are specialized knuckles used primarily in heavy-duty applications, such as construction equipment and industrial machinery. These joints are designed to handle significant loads and provide reliable performance in demanding environments.
Features of Trunnion Joints
- High load-bearing capacity
- Durable construction
- Resistant to wear and tear
- Commonly used in excavators and cranes
Trunnion joints are ideal for applications requiring robust and reliable connectivity between heavy components. Their strength and durability make them a popular choice in the construction and mining industries.
Bearing Knuckles
Bearing knuckles are specialized components that combine the functionality of bearings and knuckles in a single unit. These joints are designed to provide smooth rotational movement while maintaining structural integrity. Bearing knuckles are commonly used in steering systems and suspension systems.
Advantages of Bearing Knuckles
- Integrated bearing system for smooth movement
- Reduced friction and wear
- Improved performance and longevity
- Compact and efficient design
Bearing knuckles are essential components in modern vehicles, ensuring precise steering and suspension performance. Their advanced design makes them a popular choice for automotive and industrial applications.
Applications of Knuckles
The versatility of knuckles makes them suitable for a wide range of applications across various industries. Below are some of the most common applications of knuckles:
- Automotive steering and suspension systems
- Industrial machinery and equipment
- Agricultural vehicles and tools
- Construction and mining equipment
- Aerospace and defense systems
Each application requires specific types of knuckles, depending on the demands of the system. Understanding the unique characteristics of each type of knuckle is essential for selecting the right component for your needs.
Maintenance Tips for Knuckles
Proper maintenance is crucial for ensuring the longevity and performance of knuckles. Below are some tips for maintaining your knuckles:
- Regularly inspect joints for signs of wear and tear
- Ensure proper lubrication to reduce friction
- Check for proper alignment and clearance
- Replace worn components promptly
- Follow manufacturer recommendations for maintenance schedules
By following these maintenance tips, you can extend the life of your knuckles and ensure optimal performance in your mechanical systems.
Common Issues and Solutions
Like any mechanical component, knuckles can experience issues over time. Below are some common problems and their solutions:
- Noise or vibration: Check for proper lubrication and alignment
- Reduced performance: Inspect for worn components and replace as needed
- Leakage: Ensure seals are intact and replace if necessary
- Excessive wear: Consider upgrading to more durable materials
Addressing these issues promptly can prevent further damage and ensure reliable performance of your knuckles.
Conclusion
In conclusion, understanding the different types of knuckles and their applications is essential for anyone working with mechanical systems. From ball joints to constant velocity joints, each type of knuckle offers unique advantages and is suited for specific tasks. By selecting the right knuckle for your project and following proper maintenance practices, you can ensure optimal performance and longevity of your mechanical systems.
We encourage you to share your thoughts and experiences with knuckles in the comments section below. Additionally, feel free to explore our other articles for more insights into mechanical engineering and related topics. Together, let's continue to expand our knowledge and improve our skills in this fascinating field.

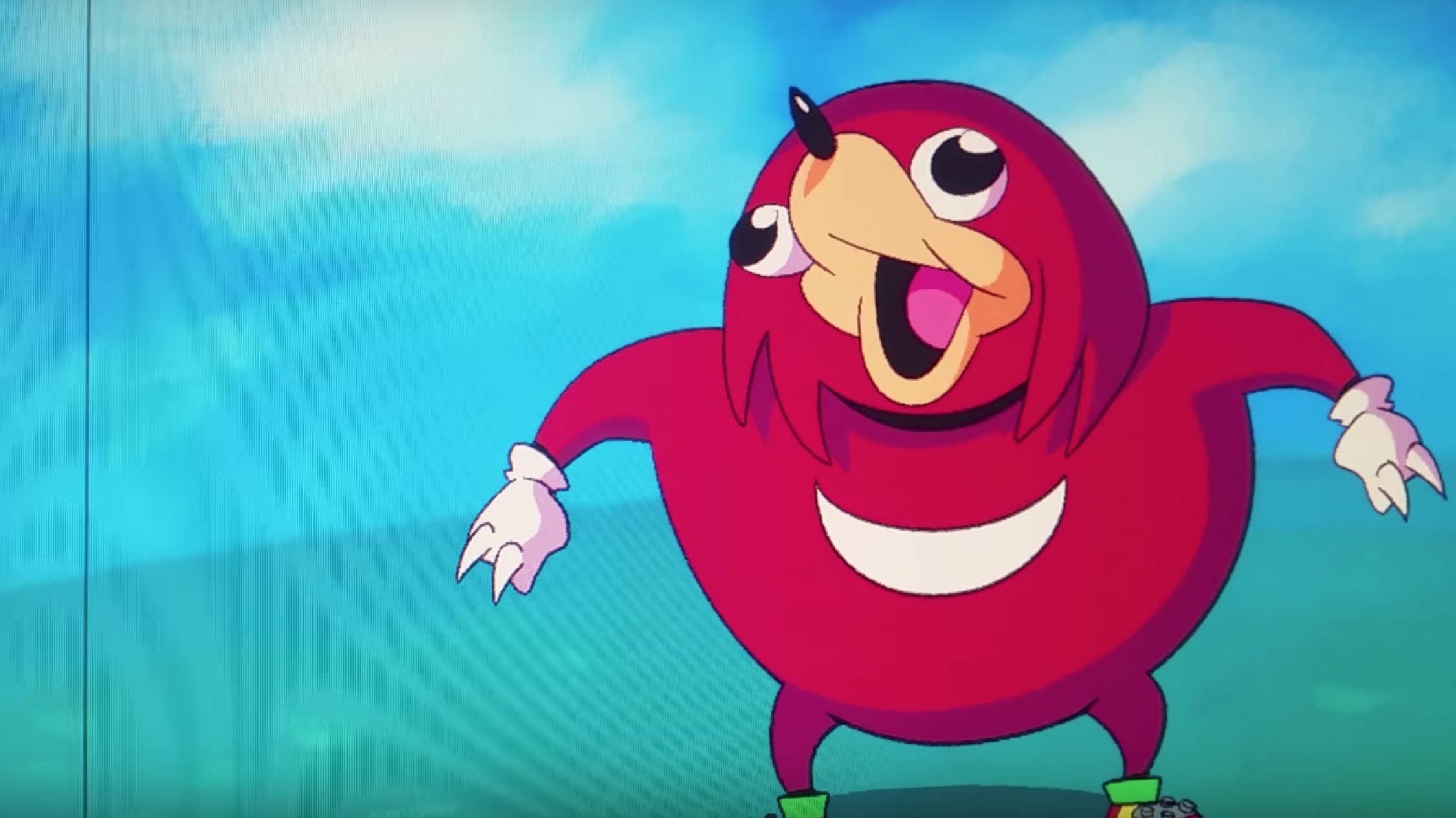
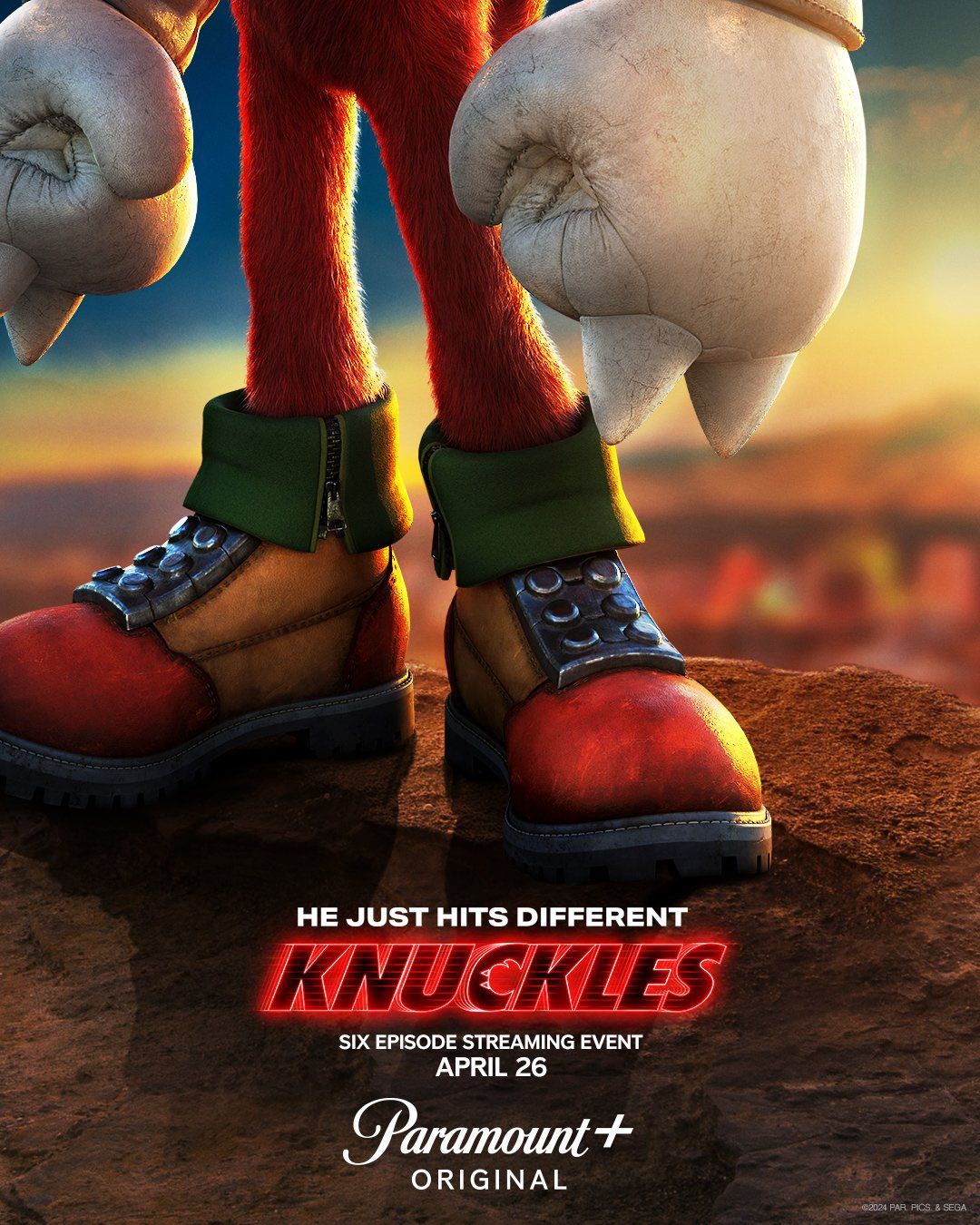